How to customize a turntable screen printer?
The turntable screen printer is more popular. It has higher efficiency and higher automation than a single workbench screen printer. The price is not particularly expensive. It is the most cost-effective screen printer. The use of the turntable screen printer is also relatively wide. As long as the product's size is not very large, the turntable screen printer can adapt to almost all types of flat products!
The following issues are mainly considered when customizing a turntable screen printer:
1) Feeding, whether the product is fed manually or automatically. If automatic feeding is used, the incoming material method of the product must be considered. If the product is more scattered, a vibration plate can be used. If the product is more regular, a conveyor belt plus a manipulator can be used.
2) Workbench, the turntable workbench will install different numbers of workstations according to the size of the product. Usually smaller products require more workstations. In addition, the product is a vacuum workbench or a T-slot workbench. The vacuum workbench is used to print relatively thin products, such as paper, film, some flexible materials, and some lightweight panels. T-slot products can be made into fixtures to fix the products. Sometimes, it may be necessary to make fixtures and vacuum devices to fix the products at the same time.
3) Prepress device. For some polyolefin materials, flame treatment devices can be installed. Some polyolefin materials are sensitive to temperature and can be treated with plasma. Many products are prone to static electricity during transportation. Electrostatic dust removal devices can be used to create good conditions for printing.
4) Positioning device: The uniformity of the printing position of the product is the most basic quality requirement. In most cases, it can be positioned by fixtures. Some products with high requirements may be positioned twice. Some glass or panels that need to be color-coded will use infrared positioning.
5) Printing device: The screen printing machine basically adopts the screen lifting method, which can be controlled by pneumatic, motor, or servo motor. Pneumatic control, the cost of the machine is lower, servo motor control, printing accuracy is higher, adjustment is more convenient, but the price will be more expensive.
The guide of the screen lifting also has a great influence on the accuracy of the machine, whether to use a guide column structure or a linear guide rail. Obviously, the guide column structure uses multiple surfaces for movement control, and its displacement error is significantly reduced. The linear guide rail has high requirements for the rigidity of the support plate, which must be flat and not easily deformed.
The movement of the turntable screen printing machine is more complicated than that of a single workbench printer. Generally speaking, the rotation of the turntable, the movement of the prepress device, the movement of the printing, and the movement of the feeding robot all need to be adjusted separately. Therefore, PLC and touch screen are generally used for control, which is convenient for the operator to adjust according to the specific characteristics of the product.
6) Unloading device: The turntable screen printing machine uses a robot for unloading. One end of the unloading robot is located above the workbench, and the other end is located above the UV curing machine or IR tunnel furnace. The robot can be pneumatically controlled or servo motor controlled. In order to maximize the function of the turntable screen printer, the use of servo robots is the main trend. There are two main structures of manipulators, suction type and grabbing type. The suction type mainly has a suction nozzle and is suitable for thin products, such as paper and panels; the grabbing type is suitable for hard products and products with complex shapes.
7) Post-printing device: The post-printing device mainly refers to the UV curing device and the IR tunnel furnace, which is used to dry the ink. The UV curing device is used to dry UV ink, and the IR tunnel furnace is used to dry solvent-based ink. The UV curing device and the IR tunnel furnace are combined with a manipulator to achieve continuous production. Some small and medium-sized enterprises may have certain requirements for the overall size of the machine due to site limitations. The tunnel furnace and UV curing device can be installed on the screen printing machine. Due to the advantages of the UVLED device in terms of size, it is more common to install the UVLED device directly on the rotary printing machine.
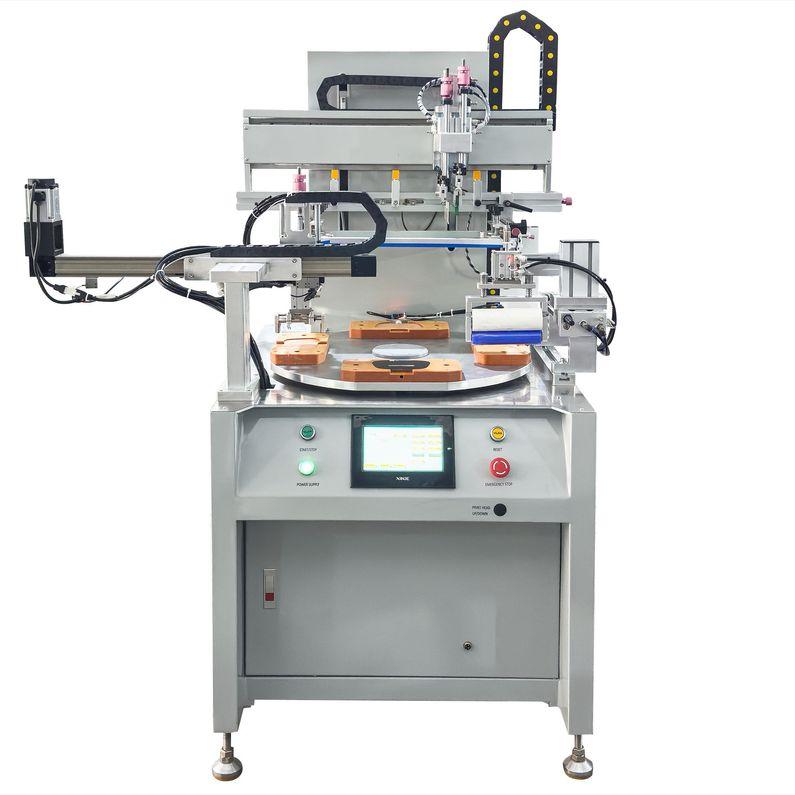